www.przemysl-polska.com
04
'19
Written on Modified on
Zadowolenie klientów zależy od niezawodności procesów obróbki
Przy planowaniu i wdrażaniu procesów obróbki skrawaniem producenci zazwyczaj koncentrują się na zmienianiu elementów swoich wewnętrznych działań. Łatwo jest wówczas stracić z oczu cel ich pracy: satysfakcję klienta.
W ogromnym stopniu satysfakcja klienta zależy od minimalizacji czasu pomiędzy złożeniem zamówienia przez klienta a dostarczeniem gotowego wyrobu. W przeszłości producenci minimalizowali czas realizacji poprzez obróbkę tysięcy identycznych części i gromadzenie dużych zapasów, z których wysyłka odbywała się natychmiastowo. Rozwiązanie typu niska różnorodność — wysoki nakład (LMHV) umożliwiało producentom terminowe spełnianie żądań klientów za pomocą stopniowego rozwijania procesu obróbki i radzenia sobie z niespodziewanymi błędami w produkcji i przerwami.Jednakże dzisiejsze wymagania rynkowe są kompletnie inne. Klienci coraz częściej zamawiają niewielkie partie produktów dostosowanych do konkretnych potrzeb. W wyniku tego producenci rzadko mają długie cykle produkcyjne. Grupy powtarzających się elementów nie są produkowane w tysiącach, ale raczej w setkach, dziesiątkach, a nawet pojedynczo. Rozwiązanie typu wysoka różnorodność — niski nakład (HMLV) nie zostawia miejsca na ciągły proces rozwoju i nieoczekiwane przerwy. Producenci są zmuszeni do opracowywania procesów obróbki skrawaniem, które są całkowicie niezawodne, już od pierwszej obrabianej części. Najważniejsze jest natychmiastowe osiągnięcie odpowiedniej prędkości, spójności i przewidywalności.
Pomimo tego wielu producentów nadal skupia się na tym, co nazywają „wydajnością”, czyli opracowaniu procesu produkcji nakierowanego niemal wyłącznie na maksymalną zdolność wytwórczą przy minimalizacji kosztów. W niezamierzony sposób ignorują prawdziwe wyzwanie, jakim jest zapewnienie satysfakcji klientów, a zwłaszcza oczekiwań klienta w zakresie terminowej dostawy.
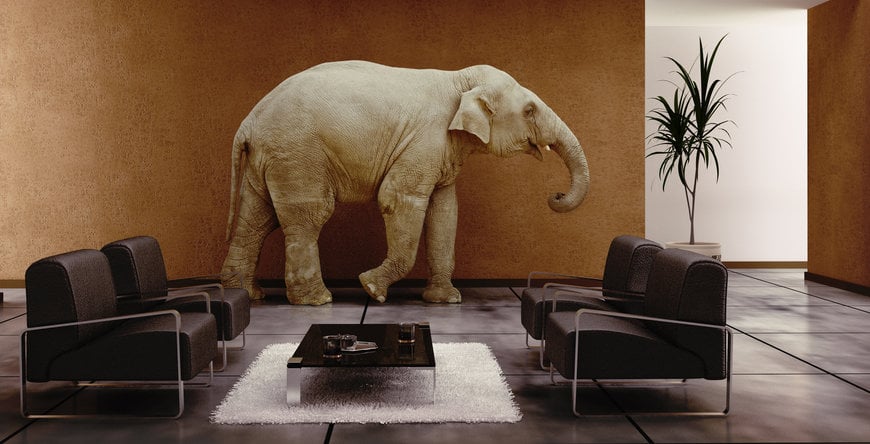
Ilustracja 1:
HQ_IMG_The_Elephant_In_The_Room.jpg
QRM
Opracowana na początku ery HMLV koncepcja QRM (Quick Response Manufacturing) podkreśla kluczową rolę, jaką w procesie produkcji odgrywa czas. Strategie QRM do spółki z działaniami mającymi na celu minimalizacją odpadów i optymalizację procesu zapewniają plan, który może naprowadzić producentów na właściwą ścieżkę do zminimalizowania czasów realizacji, a tym samym zwiększenia do maksimum zadowolenia klientów.
Rajan Suri, profesor na wydziale inżynierii przemysłowej na Uniwersytecie Wisconsin-Madison w latach 90., dostrzegł nadciągające zmiany na rynku produkcji, zwłaszcza tendencję HMLV. W 1993 r. założył centrum na rzecz QRM. Celem centrum jest utworzenie partnerstwa pomiędzy uniwersytetem a firmami wytwórczymi w celu opracowywania i wdrożenia sposobów skrócenia czasów realizacji. Strategie QRM są często stosowane jako uzupełnienie takich inicjatyw poprawiających proces produkcji jak szczupła produkcja (lead production), sześć Sigma (Six Sigma) i tym podobnych.
Podejście tradycyjne
Kierownicy produkcji w tradycyjnych środowiskach obróbki skrawaniem przede wszystkim dążą do maksymalnego stopnia wykorzystania obrabiarki. Jeżeli maszyna ma przestój, jest niewydajna, kosztuje i nie zarabia. Celem jest produkcja dużych serii na zapas. Części na magazynie stanowią bufor wobec zmiennych potrzeb klientów.
Jednakże, w przypadku produkcji HMLV, praca jest wykonywana nie w celu uzupełnienia stanów magazynowych, ale w celu zrealizowania zamówienia klienta na określoną liczbę konkretnych komponentów. Nie ma zapasów buforujących.
Dodatkowo sytuację komplikują czynniki takie jak pilne zlecenia pojawiające się w odpowiedzi na niespodziewane okoliczności lub specjalne zamówienia od ważnych klientów. Jeżeli wszystkie obrabiarki w zakładzie pracują, inne zadania muszą zostać opóźnione, aby można było się zająć pilnymi zleceniami. Wówczas opóźnione zadania same stają się pilnymi zleceniami, wydłuża się czas realizacji, a w proces produkcji zaczyna wkradać się chaos.
Kolejnym problemem jest tendencja personelu produkcyjnego do koncentrowania się na poszukiwaniu sposobów na spełnienie wewnętrznych celów, takich jak uzyskanie 100-procentowej terminowości dostaw. Planowanie często odbywa się na podstawie tych wewnętrznych celów. Na przykład, załoga warsztatu może wiedzieć, że ukończenie pewnego zadania zajmuje jeden dzień, ale przeznaczy na nie dwa dni, aby uwzględnić przerwy związane z pilnymi zleceniami i inne możliwe opóźnienia.
Planiści dodają zabezpieczenia czasowe, aby uniknąć „zarządzania akustycznego” — upomnień ze strony kierownictwa. Jednakże, jeżeli takie zachowanie jest powszechne w całym zakładzie, czas realizacji może wzrosnąć z dwóch do nawet siedmiu tygodni. Terminowe dostawy mierzone według wewnętrznych norm mogą wynosić 98%, personel produkcyjny może być zadowolony, że spełnia wewnętrzne cele, ale klient, który potrzebował produkt w ciągu dwóch tygodni na pewno nie będzie zadowolony.
Tradycyjne środowisko produkcyjne ma ograniczenia systemowe (patrz rysunek 2). Na rysunku po prawej stronie przedstawiono autostradę o minimalnym ruchu, symbolizującą niewystarczające wykorzystanie zasobów, co w przypadku produkcji oznacza wysokie koszty produkcji w przeliczeniu na gotowy element obrabiany. Nadmiernie wykorzystywana autostrada po prawej, zakorkowana stojącymi pojazdami, przedstawia chaos i wydłużone czasy realizacji w przypadku wystąpienia błędów lub niespodziewanych zadań zajmujących przestrzeń w produkcji. Środkowa ilustracja ukazuje zrównoważone i ekonomiczne podejście do wydajności i wykorzystania zasobów.
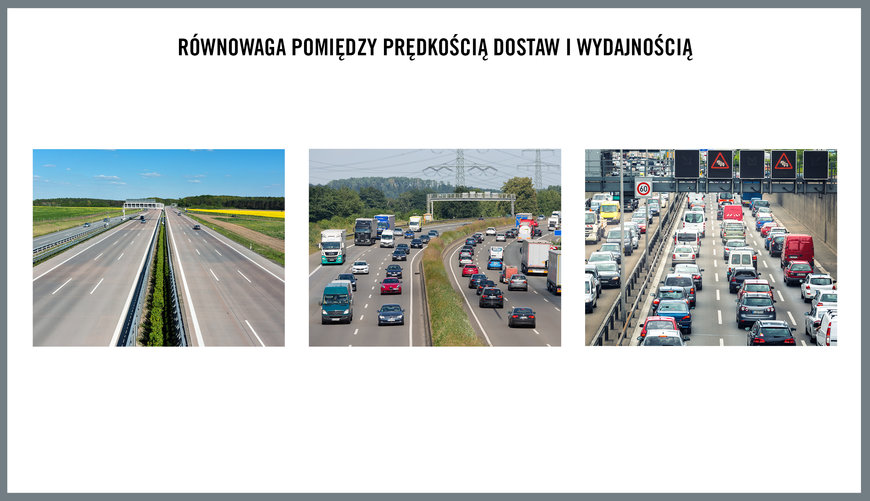
Ilustracja 2:
HQ_ILL_Balance_Between_Speed_Of_Delivery_And_Efficiency.jpg
Plan produkcji HMLV
W środowisku produkcyjnym HMLV wydajność od pierwszej części i stała jakość produkcji nieidentycznych elementów obrabianych są kluczowe. Celem jest dostarczanie produktów niestandardowych, dla których część w jednoczęściowej serii będzie kosztować tyle samo, co jedna część w serii milionowej, oraz zapewnienie natychmiastowej dostawy.
Produkcja dobrych części od samego początku zależy od ustalenia bezproblemowego i niezawodnego procesu obróbki. Obecnie modne jest wskazywanie na najnowsze techniki produkcyjne i technologie cyfryzacji jako rozwiązania problemów obróbki skrawaniem. Jednakże prędkość, spójność i elastyczność zawsze były i nadal są oparte na podstawach doskonałości operacyjnej, a także wykwalifikowanych pracownikach produkcji o pozytywnym nastawieniu i motywacji. (Patrz pasek boczny).
Przed rozpoczęciem omawiania cyfryzacji i optymalizacji, należy spojrzeć szeroko na prace warsztatowe, określić, gdzie pojawiają się straty czasu i zasobów oraz opracować metody w celu ich minimalizacji. W wyniku tego nacisk przenosi się na jakość lub niezawodność procesu.
Warsztat zero-waste
Redukcja czasów realizacji wymaga eliminacji marnotrawstwa w procesie produkcyjnym. Warsztat zero-waste nie produkuje nadmiernej ilości części, w pełni wykorzystuje materiał elementu obrabianego i eliminuje dodatkowy ruch półproduktów. Czasochłonne i marnotrawne zadania w procesie obróbki skrawaniem obejmują powstawanie zadziorów lub powierzchni o nieprawidłowej gładkości, długich wiórów, drgania i błędy obróbki, w wyniku których powstają części nie do przyjęcia. Wadliwe elementy muszą zostać poddane przeróbce lub odrzucone, co zawsze wydłuża czas oczekiwania w procesie produkcji.
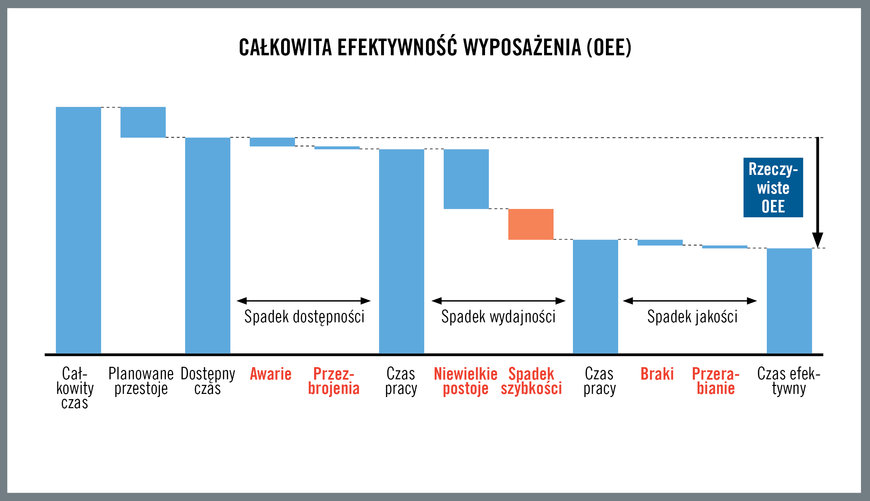
Ilustracja 3:
HQ_ILL_Overall_Equipment_Efficiency_OEE.jpg
Nawet produkowanie części o jakości, która przekracza wymagania klienta, oznacza marnotrawstwo czasu i pieniędzy. Warsztaty muszą mieć świadomość, że konieczne jest uzyskanie jak najniższej jakości elementu obrabianego, która jednocześnie jest zgodna ze specyfikacją klienta i spełnia wymagania funkcjonalne.
Jeżeli tolerancja dla części ma wynosić pięć mikronów, uzyskanie wartości trzech mikronów jest marnotrawstwem. Do uzyskania lepszej tolerancji potrzebne jest wyższej jakości oprzyrządowanie i bardziej precyzyjne procesy robocze, ale klient nie zapłaci za niezamówioną wyższą jakość. Zlecenie przyniesie straty finansowe dla warsztatu.
Poszanowanie ograniczeń
Pierwszą fazą ustanawiania zrównoważonego procesu obróbki jest dobór narzędzi o obciążalności, która spełnia lub przewyższa obciążenia mechaniczne, termiczne, chemiczne i tribologiczne występujące w trakcie skrawania metali.
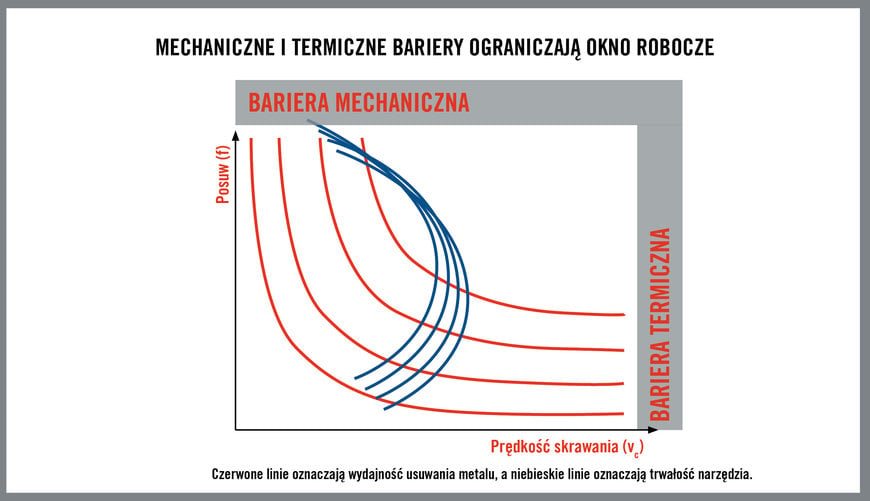
Ilustracja 4:
HQ_ILL_OS_Mechanical_And_Thermal_Barriers_Frame_Working_Window.jpg
Druga faza obejmuje dobór warunków skrawania, które odzwierciedlają ograniczenia nałożone na proces obróbki przez rzeczywiste warunki produkcji. Możliwości narzędzi skrawających są szerokie, ale konkretne realia ograniczają zakres efektywnych parametrów dla danego zastosowania.
Na przykład możliwości narzędzi zmieniają się wraz z mocą używanej obrabiarki. Charakterystyka obróbki materiału elementu obrabianego może ograniczać prędkość skrawania lub posuwu, a złożone lub słabe konfiguracje elementów mogą być podatne na drgania. Pomimo ogromnej liczby kombinacji warunków skrawania, które działają w teorii, ograniczenia narzucane przez rzeczywistość zawężą możliwość działających bezproblemowo wyborów do określonego zestawu parametrów.
Stosowanie warunków skrawania wykraczających poza ograniczenia konkretnych sytuacji będzie mieć negatywne konsekwencje, w tym wyższe koszty i niższą wydajność. Większość problemów pojawiających się podczas obróbki wynika z nierespektowania ograniczeń, które fizyczne realia nakładają na proces skrawania. Gdy warunki skrawania nie przekraczają rzeczywistych ograniczeń, operację można uznać za bezpieczną z technicznego punktu widzenia.
Jednak nie każda kombinacja warunków skrawania, która jest bezpiecznie technicznie, da taki sam wynik ekonomiczny, a zmiana warunków skrawania zmienia koszt procesu. Agresywne, ale bezpieczne pod względem technicznym, warunki skrawania spowodują zwiększenie prędkości produkowania gotowych wyrobów. Jednakże po osiągnięciu pewnego punktu, prędkość produkcji spadnie, ponieważ agresywny dobór parametrów skrawania będzie przekładał się na krótszą trwałość narzędzia, a liczne przezbrajania pochłaniają dużą ilość czasu.
W związku z tym trzeci etap osiągnięcia zrównoważonego procesu obróbki skrawaniem obejmuje określenie optymalnej kombinacji warunków skrawania dla danej sytuacji. Ważne jest, aby ustanowić domenę roboczą, w której kombinacje zapewniają odpowiednią wydajność i opłacalność. Po zastosowaniu wybranych kombinacji parametrów w produkcji zazwyczaj konieczne jest wykrywanie i usuwanie usterek w celu rozwiązania konkretnych problemów, a także ciągła analiza i optymalizacja procesu.
Wszechstronne oprzyrządowanie
Chociaż wysokowydajne, specjalistyczne narzędzia mogą zwiększyć prędkość wytwarzania, zidentyfikowanie ograniczeń procesu może naprowadzić na wybór narzędzi opracowanych z myślą o wielofunkcyjności. Jeżeli narzędzia zostaną wybrane pod względem maksymalnej wydajności i niskich kosztów obróbki skrawaniem dla danej części, zmiana konfiguracji na inną może wymagać całkowitego opróżnienia głowicy rewolwerowej obrabiarki i wymiany wszystkich narzędzi. W przypadku produkcji HMLV, w której często zmieniają się krótsze cykle różnych części, czas poświęcony na takie zmiany może pochłonąć cały wzrost produkcyjności uzyskany dzięki zastosowaniu oprzyrządowania zapewniającego maksimum wydajności.
W sytuacjach, gdy wydajność narzędzia jest zwiększona do maksimum, niektórzy operatorzy ograniczają parametry skrawania z obawy przed awariami narzędzi i przerwami. Z drugiej strony, uniwersalne narzędzia mogą być stosowane w szerszym zakresie warunków skrawania w porównaniu z narzędziami skupionymi na produktywności, chociaż przy mniej agresywnych parametrach. W przypadku zastosowania uniwersalnych narzędzi do obróbki różnych elementów sam proces obróbki skrawaniem może stać się nieco wolniejszy lub droższy, ale skrócenie czasu przygotowawczego, zmniejszenie braków i skrócenie czasu realizacji wynagradzają to z nawiązką.
Wnioski
Zadowolenie klienta to cel każdej relacji biznesowej, a kluczowym elementem satysfakcji klienta w branży wytwórczej są terminowe dostawy obrobionych komponentów. Produkcja HMLV wymaga od wytwórców, aby zoptymalizowali swoje operacje w celu skrócenia czasów realizacji i zwiększenia prędkości dostaw. Zastosowanie koncepcji QRM i zero-waste oraz wprowadzenie inicjatyw mających na celu optymalizację umożliwia wytwórcom osiągnięcie prędkości i niezawodności potrzebnych do zaspokojenia wymagań klientów w zakresie terminowych dostaw przy jednoczesnym zapewnieniu dochodowości produkcji.
(pasek boczny)
Inteligentni ludzie oraz inteligentne maszyny
Złożony i zmienny charakter produkcji HMLV wydaje się idealną okazją do wdrożenia najnowszych technologii produkcji, w tym wewnętrznej cyfryzacji z wykorzystaniem inteligentnych maszyn i analizy danych, zewnętrznej cyfryzacji za pośrednictwem zintegrowanego łańcucha dostaw i połączenia internetowego z klientami w celu skorelowania podaży i popytu. Fala nowych technologii pozornie zmniejsza wartość czynnika ludzkiego w operacjach produkcji,
ale w rzeczywistości jest wręcz odwrotnie — szybko zmieniające się elementy w produkcji HMLV zwiększają znaczenie czynnika ludzkiego. Skomplikowane operacje wymagają tradycyjnego podejścia rzemieślniczego, które obejmuje kreatywność oraz elastyczność, umożliwiającego szybką adaptację do ciągle zmieniających się części, materiałów elementu obrabianego oraz warunków skrawania.
Przede wszystkim pracownicy produkcyjni muszą myśleć pozytywnie i mieć odpowiednią motywację, aby kwestionować i rozwiązywać nowe problemy i odpowiadać na zmieniające się wyzwania, które stawia przed nimi produkcja HMLV.
Uzyskanie takiego nastawienia zazwyczaj oznacza edukację wewnętrzną, która pokaże pracownikom warsztatów, że rozwiązanie kwestii wydajności niekoniecznie musi wiązać się z dużymi kosztami i zaawansowaną technologię. Nastawienie obejmuje zdawanie sobie sprawy z kluczowości zadowolenia klienta. Nauki zdobyte podczas doskonalenia operacji lub grupy operacji mogą zostać zastosowane ponownie i rozszerzone, aby obejmować podobne przypadki w całym zakładzie.
Doświadczenie z hali produkcyjnej może zostać uzupełnione o zorganizowane inicjatywy edukacyjne, takie jak program STEP (Seco Technical Education Program) — dobrze opracowany i praktyczny program stworzony z myślą o zapoznaniu użytkowników z najnowszymi technikami i systemami oprzyrządowania.
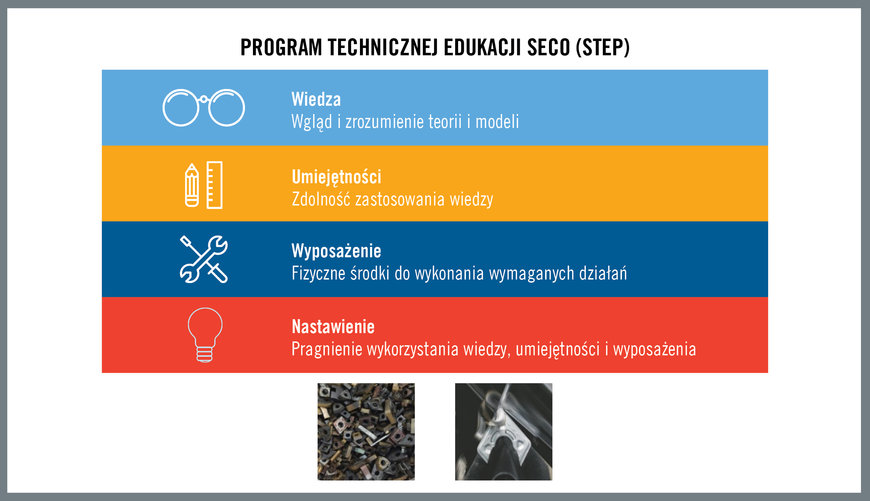
Ilustracja 5:
HQ_ILL_Seco_Technical_Education_Programme.jpg
Połączenie doświadczenia praktycznego w analizie procesu i doskonalenia z wykorzystaniem zorganizowanych programów edukacyjnych to klucz do ustanowienia kultury rozwiązywania problemów i doskonalenia procesów, która będzie zapewniać ciągły sukces produkcyjny. Edukację dopełniają interaktywne zasoby informacyjne, takie jak portal cyfrowy Seco My Pages, strona internetowa stworzona w celu ułatwienia zamawiania i dostawy narzędzi, pomocy w znalezieniu lepszego sposobu zastosowania narzędzi, optymalizowaniu procesów i uzyskiwaniu pomocy ze strony inżynierów.
Maksymalizując korzyści z obróbki skrawaniem HMLV, kierownictwo musi odejść od ograniczeń systemowych tradycyjnej obróbki wysokonakładowej. Ważne jest, aby skoncentrować się na wzmocnieniu roli pracowników w osiągnięciu odpowiedniego nastawienia i kreatywności potrzebnej w ustaleniu równowagi pomiędzy wydajnością a elastycznością produkcji, która nieustannie będzie zapewniać całkowitą satysfakcję klienta.
Autor:
Patrick de Vos, starszy specjalista ds. doradztwa i kierownik programów edukacji technicznej w firmie Seco Tools